
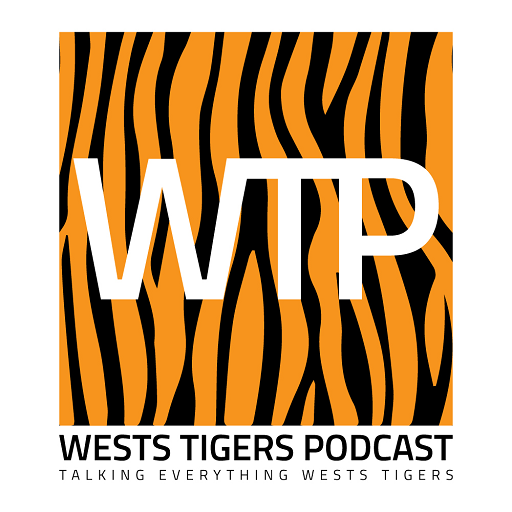
If not, then oxygen in the air will react to form detrimental oxide inclusions in the steel.įigure 2. To produce higher quality product, the liquid steel must be protected from exposure to air by a slag cover over the liquid surface in each vessel and by using ceramic nozzles between vessels. If solid inclusion particles are allowed to remain in the product, surface defects such as “slivers” may form during subsequent rolling operations or local internal stress concentration may occur, leading to a reduction in fatigue life. The tundish can also serve as a refining vessel to float out detrimental inclusions into the slag layer. The tundish holds enough metal to provide a continuous flow to the mold, even during an exchange of ladles, which are supplied periodically from the steelmaking process. In this process, molten steel flows from a ladle, through a tundish into the mold. 1 (second frame) and the close-up of the upper mold region is shown in Fig. The continuous casting process for steel is shown in Fig. Many other developments and innovations have transformed the continuous casting process into the sophisticated process currently used to produce over 90% of steel in the world today, including plain carbon, alloy, and stainless steel grades ( Wolf 1992). This problem was overcome by Junghans in 1934 by vertically oscillating the mold, utilizing the concept of “negative strip” where the mold travels downward faster than the steel shell during some portion of the oscillation cycle to dislodge any sticking ( Wolf 1992). Earlier attempts suffered from technical difficulties such as “breakouts,” where the solidifying steel shell sticks to the mold, tears, and allows molten steel to pour out over the bottom of the machine. Although the continuous strip casting process was conceived by Bessemer in 1858, the continuous casting of steel did not gain widespread use until the 1960s. Thomas, in Encyclopedia of Materials: Science and Technology, 2001 1 Steel Continuous CastingĬontinuous casting is a relatively new process in historical terms. The major unresolved issues in the technology are the details of operating cost and the technology necessary to develop conventional rolled properties from a cast structure.ī.G. This is significantly less than any competing technology. The investment cost for a direct strip casting plant is estimated at 100 million dollars for a production rate 6×10 5 tonnes per year. Twin-roll strip casting has the potential to allow a significant simplification of the steel solidification process as it enables coiled steel strip production without the necessity for a hot strip mill.
#Stripes cast plus#
They are 15 tonnes in weight, 2 mm thick with a longitudinal thickness variation of plus or minus 50 microns and have a positive crown of less than 60 microns. 1 rank as three of the best castings made.

This technology is the result of twenty years of development in both Japan and Australia and is the first casting machine for ferrous materials that must also produce a product with similar dimensions to a hot-rolled product. An example of direct strip cast low-carbon steel coils (courtesy of BHP, Australia).
